PROJECT BACKGROUND
In 2019, Delaware Solid Waste Authority (DSWA) began testing Warren Environmental’s (Warren) epoxy solutions for their leachate collection system manholes at the Pigeon Point Landfill in New Castle, Delaware. As a part of the testing initiative, A&W Coatings was tasked with lining three manholes at the landfill to evaluate the product’s rehabilitation performance under live conditions.
The Warren + A&W team was recommended by an industry reference with experience installing Warren’s epoxy system and had observed the condition of DWSA’s manholes. Working together to provide education on the benefits of protective coatings and successful applications, using trenchless technology as a rehabilitation solution was attractive to the owner because excavation and replacement could be a major challenge with manholes as deep as 80 vertical feet (VF) in their system. DWSA needed a timely, full-proof solution to rehabilitate its system’s manholes, protect them from corrosive chemicals, and extend their service life.
The manholes were highly corroded and severely deteriorated from years of exposure to corrosive chemicals from the landfill’s leachate. Leachate is a toxic liquid formed when rainwater filters through waste in a landfill. Carried through pipes and manholes, leachate is highly corrosive to unprotected concrete. It was important for the owner to test a solution under live conditions because managing corrosive leachate is a continuous problem in landfills. As landfills grow larger, owners are required to add manhole sections to make them taller, so they are not buried by new media dumped on the landfill. As manholes get deeper, they become more challenging to repair because they are susceptible to more live loads from the soil and debris surrounding the structures and have more exposure to groundwater infiltration. Deep manholes also have higher water pressures applied to the structure and coating. If left unprotected from chemical attack, these manholes continue to erode and lose their structural value. A&W’s expert application of Warren’s epoxy coatings would provide the best value solution to solve this problem for the owner. With a single coat, Warren’s epoxy could structurally enhance the host structures and protect them from future corrosion.
SCOPE OF WORK
The A&W crew mobilized to the site to begin the project in October 2019. The scope of work included the surface preparation and lining of three 48-inch leachate manholes varying in depth from 11 to 22 VF. Surface preparation prior to the coating activities included high-pressure washing at 5,000 pounds per square inch (psi) using a vac truck to remove a thick layer of buildup and associated debris found in the manholes. When infiltration was discovered in one of the manholes, A&W applied Warren’s 151-HG hydrophobic grout through injection to stop the leak through drilled grout ports. Once the 151-HG grout had set and successfully stopped the infiltration, the manhole was rinsed with muriatic acid, bleach, and potable water. With all pre-coating activities complete, A&W lined the manholes and flow channels with 250 mils of Warren’s 301-14 high performance epoxy.
Following the epoxy application, adhesion and spark testing were performed per Warren’s specifications. Eight adhesion tests were conducted, and Warren’s epoxy exceeded the minimum value of 300 psi. A&W successfully completed the project just four days later, on schedule and within the owner’s budget. Delivering this trenchless technology solution on time was important for DWSA’s evaluation because it could be used as a potentially viable solution for their additional manholes on a future project.
PROJECT CHALLENGES
Working in deteriorated manholes within an active landfill with a potentially hazardous atmosphere was the biggest challenge presented by the location, making safety the most important factor in this project. Toxic gases in the atmosphere were more abundant in this type of system than those found in a municipal wastewater system, calling for extra precautions. In some cases, A&W’s gas meters testing for hazardous atmosphere would alarm at ground level outside of the confined space. To address this challenge, A&W supplied air and robust ventilation systems to the spray technicians, especially during the initial cleaning process when more hazardous gasses were released from the compromised concrete. To the project’s advantage, A&W had decades of experience working in confined spaces to understand and overcome the hazards present when working in deep shafts and the toxic ambient air conditions created by the work environment.
ADDITIONAL PHOTOS

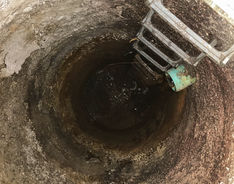


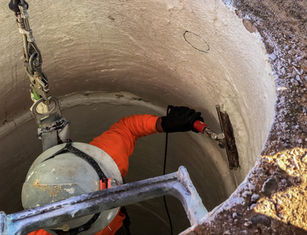

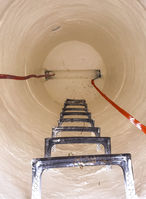


PROJECT SUCCESSES
This project was a success because A&W worked with the plan presented and completed the work safely under the supervision of the engineering firm. To ensure that DSWA’s testing initiative was a success, it was important for the Warren + A&W team to deliver on high expectations regarding the application, safety, and product quality. The team’s expertise in rehabilitating heavily corroded infrastructure in dangerous conditions made a seemingly difficult project easy, providing the owner with a sound rehabilitation solution that would protect their manhole structure for decades to come.